
When I first saw the DV8 bumper, I was instantly sold. I wanted a high-clearance, hidden hitch, tucked-in bumper that was simple. I really liked the JCR bumper for a while, but their design counts on people using their swingouts, so it sticks out a lot. I'm going for less ass.
The DV8 bumper had almost everything I wanted in terms of its fundamental shape, but it was missing a few key things:
No sensor cutouts
No recovery points
Included hitch receiver is bush league
Only 3 bolts per frame mount
Powder coating was really rough, difficult to clean
Still, I wanted the look of the bumper and was willing to make some modifications, rather than start from scratch building one myself, which was my original plan.

Bumper Modifications
I added two clevis mounts by cutting through the bumper. These are welded on the exterior of the bumper and through a window cut-out on the bumper's mounting plate. In order to shore things up a bit, I drilled and tapped for a 1/2in bolt, which was welded into the back of the clevis mount. So, these are welded in 2 places and attached to the frame brackets via a 1/2in bolt. Not sure if that's substantial enough - a total amateur (me) did the welding - but I feel reasonably good about it.
I also cut 4 holes (7/8 hole saw) for sensors. The sensor bezels transferred over from the stock bumper just fine, but required a little dremel trimming on some little plastic tabs to fit flush. Still can't understand why DV8 wouldn't cut holes for these. And yes, they work just fine.
Bracket Modifications
The DV8 mounting brackets that attach the bumper to the frame were modified to allow for the clevis mount's 1/2in bolt. I used the same hole saw to cut a window here. Getting this bolt tight after installation is an absolute nightmare (think 1/16 turn at a time x100), but I feel more confident about the recovery points now, so it was worth it.
I also thought it didn't make any sense that there were only 3 bolts on each bracket which attach to the bumper. I cut and threaded for another 1/2 bolt on the bumper mount plate, threw on a nut from the inside (used the front-facing hole I cut for the clevis prior to welding it in place) and then welded it.
Maybe a 4th bolt doesn't matter that much, but with the bumper now having 2 recovery points, I wanted to ensure that thing was as attached to [the thing that's actually attached to] the frame as possible. I think the weak point here is the frame bracket itself. If something bends or breaks, I think it will be the rear-facing plate of the DV8 bracket.

Hitch Receiver Modifications
I knew I was going to replace the hitch before ordering. It's billed as an "accessory hitch" which likely translates to "bike rack holder." Looked like something you might get on a RAV4 (see attachment points below). I tossed that, got a massive Curt hitch receiver, and welded a bracket system around it (see finished product above).
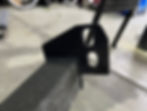
This whole project was my first time welding anything (after countless hours of practicing, of course). The hitch was entirely designed around that lack of skill, so everything has a failsafe. In short, I took 3 pieces of 3/16 steel (x2) and created brackets that would fit around the DV8 frame brackets. Then, I cut-out sections of the Curt hitch receiver to get the height right and welded the brackets to the hitch receiver.
Two examples of failsafe measures:
The brackets I welded don't rely solely on the welds. For the two upright walls of the bracket, I cut 2 slim windows in them, and then the bottom/flat piece of the bracket was cut to slide into those windows (notice the gaps in the picture). So, if all of those welds failed, it's still a sheet of steel sitting within (not below) 2 other pieces of steel.
Where the hitch receiver attaches to the brackets I made, I left enough material on the bracket walls to weld and bolt on a ~1" piece of steel beneath the hitch receiver (see picture for area beneath the hitch receiver). This way, if literally every single weld I made failed, I've got four 1/2in Grade 8 bolts keeping the receiver from falling off and injuring another driver.
This receiver modification was really time-consuming. But, totally worth it. The one that came with it wouldn't have been capable of pulling much, and I'd still like a camping trailer one of these days. I have no idea what this new design would actually be rated for, but I can say with confidence that it's over-the-top burly design would clearly seem even as substantial as what you'd see on an F-350.
Still not going anywhere without my hitch-mounted D-ring though ;-)
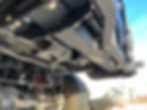
Ignore the electric tape on the trailer harness- trying to figure out how I want to attach that.
Installation Notes and Lessons Learned
Not gonna lie; the install sucked. I decided to attach the bumper to the DV8 brackets and get that on the truck, then carefully add the hitch receiver. It fit, barely. Lots of wood stacked on a jack, moving temporarily-installed bolts, etc.
I designed all of this to suit my needs and knew the install would be a challenge (due almost entirely to the clevis 1/2in bolts), but I was happy with the design. I'm sure someone else could do a better job with the hitch receiver design. Only thing I wish I had done differently is I wish I had cut about 1/2 an inch off of the clevis mounts so they didn't stick out quite as much.
I learned a lot in this process, but what I found to be most challenging was cutting-out rectangular holes/window in 3/16 steel. All of mine have a bit of a weird shape to them. They work, so it's fine, but that was really hard. The other big learning was to leave just a bit more tolerance in the design. Maybe for something similar I'll throw a washer in somewhere as a spacer when I'm planning on fitment.
Powder Coating
Naturally, after all of those modifications and a newly-created hitch receiver system, I needed to get it power coated. Took it to Accurate Powder Coating in Arvada, CO, which I've used before and they're great. They recommended a textured finish which is kind of a satin but still retains aspects of texture (and that's great, because it slightly masks some of my not-so-amazing-looking welds). 10x easier to clean than what DV8 had on it. Absolutely love this finish.

What's Next?
I'm going to cut the body right along the plastic trim piece, then make a slider of sorts that gives me some protection between the rear tires and the bumper. Old picture above, but you get the idea.
Eventually I may move the license plate back down to the bumper, too.